The fiber properties likely to affect the degree of fiber entanglement in a tuft, and therefore, nep formation, are
1. fineness (diameter and length, i.e., aspect ratio)
2. crimp level
3. impurity content of the baled mass (not strictly a fiber property but dependent on grade)
Townend23 reports that, for a fixed diameter, longer fibers have a greater tendency to form neps in worsted carding. This is because longer fibers have a greater probability of being broken, the recoil of the shorter length causing it to become entangled into a nep. By analyzing neps, Alon and Alexander21 found that, in carding 50-mm 3.3-dtex acrylic fibers, 28% of the fibers forming neps were short, broken fibers, whereas, in the associated card sliver, only 7% of fibers could be classified as short fibers, and only 2% in the bale raw stock. Based on Alon and Alexander’s observation, we may assume that around 72% of the fibers forming neps were either the longer lengths of the broken fibers or entanglement of these with unbroken fibers. They report that the number of fibers found to constitute a nep varied from 5 in a small nep to 24 in a large one. Neps were identified as having a dense center where one or more fibers were located that initiated the nep formation. These fibers were looped or had very complex knot configurations and could be short broken lengths or longer fibers.
Although the above discussion is about fiber length, we must remember that an important factor in nep formation is the buckling of the fibers, either by the effect of rolling or by the sudden release of tensile stress. Therefore, in addition to length, other important fiber characteristics are elastic modulus and fiber fineness. Alon and Alexander found that the propensity for fibers to form neps is related to a buckling coefficient,
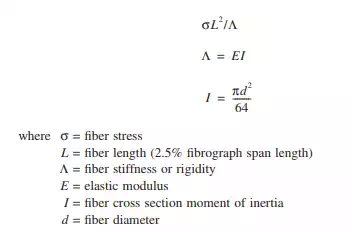
For a range of cottons, a definite linearity was found between measured neps per gram in the cotton slivers and the buckling coefficients of the cottons.21 Clearly, stiffer fibers should have a lower nep propensity. Thus, the parameters within the buckling coefficient that combine to have the greatest effect on nep formation are fiber diameter and elastic modulus. Fiber diameter also controls the number of fibers entangled in a given tuft size, i.e., mass. We learned in Chapter 1 that, within a cotton variety, fineness and maturity are represented by micronaire; the higher the micronaire, the coarser and more mature the fiber and the greater its rigidity. Figure 3.24 shows that, as the micronaire of cottons increases, the nep level of a card web decreases.15,16 Immature cotton fibers have low micronaire values, and Gulati and Ahmed26 and Pryor and Elting27 observed that neppiness was significantly correlated with the number of immature fibers in a cotton mass.
Evenson28 considers the variation in fineness and maturity within a given grade to be of equal importance. Blending with higher micronaire cottons can therefore reduce nep levels. Table 3.5 shows a similar trend for wool and mmf with respect to fineness.23 Table 3.6 indicates that nep levels increase with the degree of fiber crimp. The higher the crimp level, the greater will be the entanglement within fiber tufts and the more severe the shear action required to individualize fibers causing fiber breakage and associated neps.