It is the size of macromolecules that gives them their unique and useful properties. Size allows polymer chains to act as a group so that when one part of the chain moves the other parts are affected, and so that when one polymer chain moves, surrounding chains are affected by that movement. Size allows memory to be imparted, retained, and used. Size allows cumulative effects of secondary bonding to become dominant factors in some behavior. Thus, the determination of a polymer’s size adds an important factor in understanding its behavior. Generally, the higher the molecular weight, the larger the polymer.
The average molecule weight (M) of a polymer is the product of the average number of repeat units or mers expressed as n¯ or DP times the molecular weight of these repeating units. M for a group of chains of average formula (CH2 CH2)1000 is 1000(28)
28,000. Polymerization reactions, both synthetic and natural, lead to polymers with heterogeneous molecular weights, i.e., polymer chains with a different number of units. Molecular weight distributions may be relatively broad (Fig. 3.1), as is the case for most synthetic polymers and many naturally occurring polymers. It may be relatively narrow for certain natural polymers (because of the imposed steric and electronic constraints), or may be mono-, bi-, tri-, or polymodal. A bimodal curve is often characteristic of a polymerization occurring under two distinct pathways or environments.
Most synthetic polymers and many naturally occurring polymers consist of molecules with different molecular weights and are said to be polydisperse. In contrast, specific proteins and nucleic acids, like typical small molecules, consist of molecules with a specific molecular weight (M) and are said to be monodisperse. Since typical small molecules and large molecules with molecular weights less than a critical value (Z) required for chain entanglement are weak and are readily attacked by appropriate reactants, it is apparent that the following properties are related to molecular
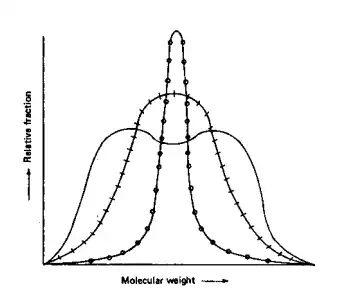
weight. Thus, melt viscosity, tensile strength, modulus, impact strength or toughness, and resistance to heat and corrosives are dependent on the molecular weight of amorphous polymers and their molecular weight distribution (MWD). In contrast, density, specific heat capacity, and refractive index are essentially independent of the molecular weight at molecular weight values above the critical molecular weight.
The melt viscosity is usually proportional to the 3.4 power of the average molecular weight at values above the critical molecular weight required for chain entanglement, i.e.,
M3,4. Thus, the melt viscosity increases rapidly as the molecular weight increases and more energy is required for the processing and fabrication of these large molecules. However, as shown in Fig. 3.2, the strength of polymers increases as the molecular weight increases and then tends to level off. Thus, while a value above the threshold molecular weight value (TMWV; lowest molecular weight where the desired property value is achieved) is essential for most practical applications, the additional cost of energy required for processing extremely high molecular weight polymers is seldom justified. Accordingly, it is customary to establish a commercial polymer range above the TMWV but below the extremely high molecular weight range. However, it should be noted that since toughness increases with molecular weight, extremely high molecular weight polymers, such as ultrahigh molecular weight polyethylene (UHMPE), are used for the production of tough articles such as trash barrels. Oligomers and other low molecular weight polymers are not useful for applications where high strength is required.
The word oligomer is derived from the Greek word oligos, meaning “a few.” The value for TMWV will be dependent on Tg, the cohesive energy density (CED) of amorphous polymers (Sec. 3.2), the extent of crystallinity in crystalline polymers, and the effect of reinforcements in polymeric composites. Thus, while a low molecular weight amorphous polymer may be satisfactory for use as a coating or adhesive,
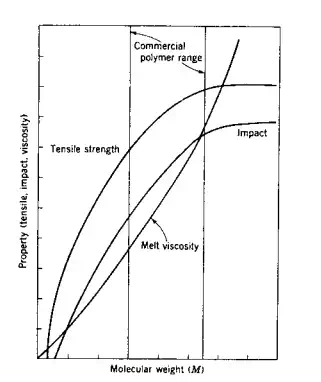
a DP value of at least 1000 may be required if the polymer is used as an elastomer or plastic. With the exception of polymers with highly regular structures, such as isotactic polypropylene, strong hydrogen intermolecular bonds are required for fibers. Because of their higher CED values, lower DP values are satisfactory for polar polymers used as fibers.
Comments are closed.