In conventional ring spinning, fibres in the selvedge of strand emerging from front roller nip do not get fully integrated into the yarn because of the restriction to twist flow by the spinning triangle. These fibres show up partly as protruding hairs or as wild fibres.
The spinning triangle exists because of higher width of the strand as compared to final yarn diameter. Further the fibres are tensioned to varying extent depending upon their position in the spinning triangle. As a result full realization of fibre strength is not achieved in the yarn.
The hairiness gives a rough feel to the yarn. Variation in hairiness is a source of weft bars and warp way streaks in the fabric. Long protruding hairs from the yarn contribute to multiple breaks in weaving and fabric faults like stitches and floats.
This problem is solved by applying the compact spinning systems that increases yarn quality. It is carried out by means of narrowing and decreasing the width of the band of fibres which come out from the drawing apparatus before it is twisted into yarn, and by the elimination of the spinning triangle. It can be used for spinning both short and long staple yarns.
The compact spinning process produces a new yarn structure, which approaches the ideal staple fibre yarn construction even more closely. This has positive effects on raw material use, productivity, downstream processing, and on the product appearance.
Factors Affecting The Spinning Triangle
The twist that is transmitted to the yarn in the ring spinning process originates along the curve between the traveler and front drafting rollers. Transmission of twists is opposite to the yarn movement in this area. The traveler transmits twists to already drafted fibres as close as possible to the clamping point after the front rollers. However, the twists never reach the clamping point, because after leaving the front rollers the fibres tend to direct towards yarn axis. The different lengths of the path of the inner and outer fibres that form the yarn cause a spinning triangle in ring spinning.
If the spinning triangle is too short (a), then the fibres on the edge must be strongly deflected to bind them in. This is not possible with all fibres, and lost as fly. Thus with shorter triangle, smaller weak point resulting into fewer end breaks but makes the yarn hairy. On the other hand, a long spinning triangle (b) implies a long weak point and hence more end breaks giving smoother yarn and less fly.
The length of the spinning triangle depends on spinning geometry and twisting intensity. The form and dimensions of the spinning triangle significantly influence the structure, surface characteristics, physical and mechanical characteristics of spun yarn. Not all fibres that are placed at the external edges of the triangle can be spun into the yarn structure, and can leave the drafting equipment without having been spun into the yarn. Such fibres also increase yarn hairiness.
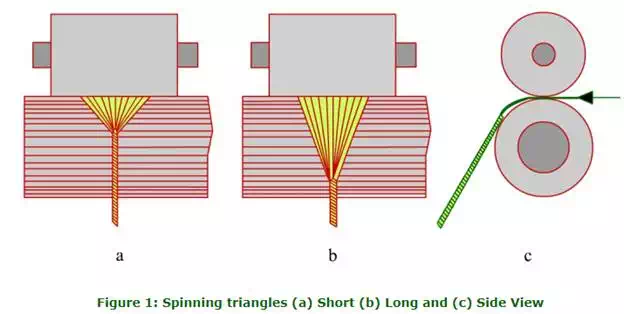
The spinning triangle is the critical weak spot of the spinning process. The spinning triangle prevents the edge fibres from being completely incorporated into the yarn body. However, in compact spinning, the drafted fibres emerging from the nip line of the front roller of the drafting arrangement are condensed in a line.