It can be reasoned that to obtain a high degree of fiber parallelism in a yarn, the fibers must be already straight and parallel in the fiber assembly presented for consolidation by twist or some other means. Figure 1.8 shows the process sequence for the manufacture of the more common types of staple-spun yarn. When fibers are first purchased for conversion to yarns, they are usually obtained in large fiber bales. At this stage, the fibrous mass is referred to as the raw material; some raw material may be waste for recycling. In the raw material state, fibers have no definite orientation or configuration. A high proportion will be entangled and, in the case of natural fibers like cotton and wool, dirt and vegetable particles and other impurities (e.t., grease) will be present.
The first stage in a yarn production process is therefore the cleaning and disentangling of the raw material. Where grease has to be removed, the material is scoured. The disentangling of the fiber mass occurs progressively using pin or saw-tooth wire-covered rollers. The earlier stages are collectively referred to as opening and cleaning, since, as the compressed fiber mass is opened up, solid impurities are released to become waste. The final stage of disentanglement is called carding, where the fiber mass is separated into individual fibers that are collected together to form a twistless rope termed a card sliver.
Because of the carding process, the fiber orientation is very close to the sliver axis; therefore, carding may be considered as the start of the parallel arrangement of fibers. However, only very few fibers in a card sliver have a straightened shape. To straighten hooked and folded fibers, and greatly improve fiber alignment along the sliver axis, the sliver is thinned by stretching; the mechanical action is called drafting, and the amount by which it is stretched is the draft. Clearly, the count of the sliver will decrease, so drafting is an attenuating action, and the draft is equal to the factor by which the sliver count is reduced
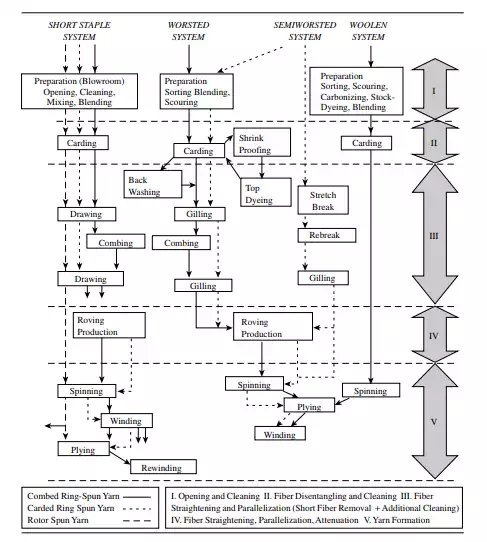
is reduced by a draft of 3, a 1-m length would be stretched to 3 m, and the resulting sliver count would be 2 ktex. This means that

The drafting of the sliver gives rise to shear within the fiber mass; fibers slide past each other as the sliver is stretched, giving the permanent extension or elongation. The friction contact between fibers during the sliding motion straightens and aligns fibers along the sliver axis. Figure 1.9 shows the situation where two pairs
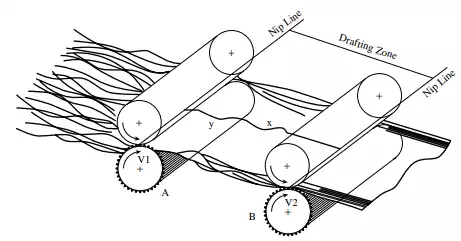
of rollers are used for drafting. The bottom rollers are fluted metal rollers that are driven through a set of gears by an electric motor. The flutes may be straight, as illustrated in Figure 1.9, or given a slight spiral. The top rollers are synthetic-rubbercovered rollers and are pressured down onto the bottom rollers (termed weighted down) and driven through frictional contact. The compression, referred to as the hardness, of the synthetic rubber cover can be varied to suit the fiber frictional properties. The flutes of the bottom rollers and the resilience of the top rollers are important for the nipping of fibers during drafting.