Straightening the yarn length to measure the diameter involves tensioning the yarn, which also narrows the cross section by bringing fibers into closer contact and increasing the packing density. Although there are test methods6 for yarn diameter measurements that attempt to circumvent these difficulties, they are not appropriate for use in the commercial production of yarns. Also, in spinning yarns, there is no direct relationship between spinning variables and yarn diameter, so it is not the practice to set up a spinning machine to produce a specified yarn diameter. A more useful and practical measure that indirectly gives an indication of yarn thickness is a parameter that is termed the yarn count or yarn number.
The yarn count is a number giving a measure of the yarn linear density. The linear density is defined as the mass per unit length. In Système International (SI) units, the mass is in grams, and the unit length is meters. In textiles, a longer length is used for greater meaningful measurements, since this would average the small, random, mass variations along the length that are characteristic of spun yarns. There are two systems by which the count is expressed, as described below.
• Direct system. This expresses the count as the mass of a standard length. The mass is measured in grams, and the specific length is either 1 km or 9 km.
• Indirect system. This gives the length that weighs a standard mass. The standard mass is either 1 kg or 1 lb, and the associated length is, respectively, in meters or yards. Usually, thousands of meters of a yarn are required to weigh 1 kg and, similarly, thousands of yards to weigh 1 lb.
This makes measurements and calculations cumbersome. To circumvent any such awkwardness, a standard length is used. The standard length can be 1 km, 840 yd, 560 yd, or 250 yd. The standard lengths in yards are commonly called hanks, or some cases skeins. Thus, we can now say that the indirect system gives the number of kilometers that weigh a kilogram (metric units) or the number of hanks that weigh one pound (English Imperial units). The type of hank being referred to depends on the type of yarn or, more correctly, the manufacturing route used to produce the yarn. For carded and combed ring spun yarns, an 840-yd hank is used; a 560-yd hank is associated with worsted and semiworsted yarns, and a 256-yd hank with woolen yarns.
Generally, cotton fibers are made by the carded and combed ring spun yarn routes, and synthetic fibers of similar lengths to cotton are made by the carded ring spun route, whereas wool and similar lengths synthetics are processed by the worsted, semi-worsted and woolen routes. With respect to the unconventional processes, if a fiber type spun by any of these systems can be also spun by one of the conventional systems, the hank associated with that conventional route is used. For example, the production of rotor spun yarns is usually from cotton and synthetic fibers of cotton lengths, and the 840-yd hank is therefore used. Repco yarns can be made of wool or synthetic fibers of wool lengths, and the 560-yd hank is the applicable standard length. Table 1.3 summarizes the most commonly used units of count for the direct and indirect systems.
A more comprehensive list can be found in a publication by The Textile Institute, “Textile Terms and Definitions,”4 and a number of the references cited at the end of this chapter give a brief account of the historical origins of several units of the indirect system.
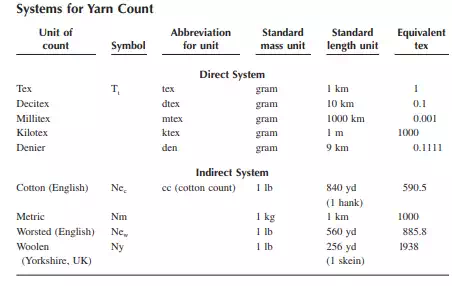
Although all the units of count in Table 1.3 are used in practice, we shall use only the tex throughout the remaining chapters of this book. The table gives the conversion factors in relation to tex. A clear advantage of the tex is that we can refer to multiples and decimal fractions of the tex in terms of the base 10 scale. Thus, 1000 tex = 1 kilotex (ktex), 0.1 tex = decitex (dtex), and 0.001 tex = millitex (mtex). In this way, the tex unit can be used for fibers and yarns. Hence, if we have a yarn of 100 tex spun from fiber of 1 dtex (0.1 tex), we can estimate the number of fibers in the yarn cross section to be 1000. A 50-tex yarn should be half the size of a 100- tex, requiring only 500 fibers in its cross section. It is the practice to refer to the dtex of a fiber as the fiber fineness; the denier (den) is also used to express fiber fineness. A fiber fineness of 1.5 den is therefore equivalent to 1.7 dtex.
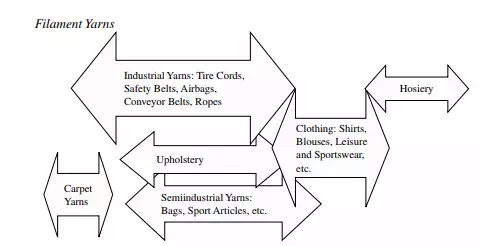
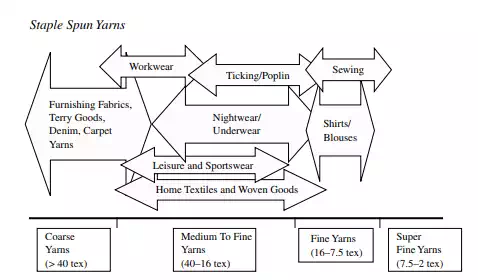
apparel. Spun staple yarns hold a principal position in the market for shirts, blouses, home textiles, bed linen, trousers, suits, and so on. Filament yarns are highly competitive in the carpet-yarn and sportswear sectors and in the industrial yarn area for technical textiles