‘Drive systems’ in Ring Spinning machine, the mechanism used for building the ring frame packages, known as cops, was discussed. But, the actual yarn placement inside the package was not discussed in that lecture. It is important to understand this, since it will affect the unwinding behavior of these packages in the next step, namely the winding. Hence, the structure of the cops is discussed in detail.
Build of cops
The cop as shown in Figure.1 comprises of three visually distinct parts – the barrel like base A, the cylindrical middle part W, and the conically convergent tip K. It is built up from bottom to top from many conical layers as shown in Figure.2, but constant conicity is achieved only after the formation of the base.
In the base portion itself, winding begins with an almost cylindrical layer on the cylindrical tube. The initial layers are conical in shape, thicker at the base and thinner at the tip. With the deposition of one layer on another of these conical layers, the conicity gradually increases.
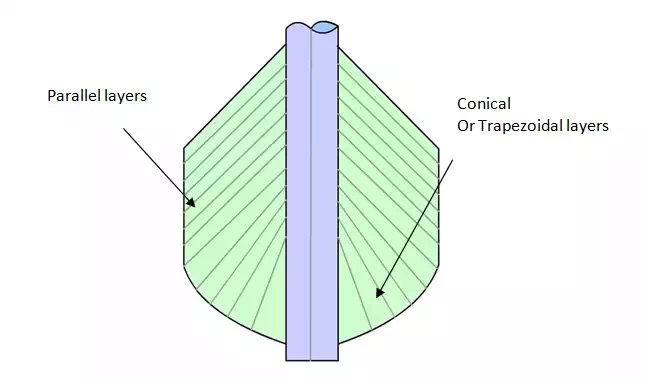
Each layer comprises a main layer, also called as winding layer and a cross-layer, also called as binding layer which are shown in Figure 3. The main layer is formed during slow raising of the ring rail, individual coils being laid close to each other or on each other.
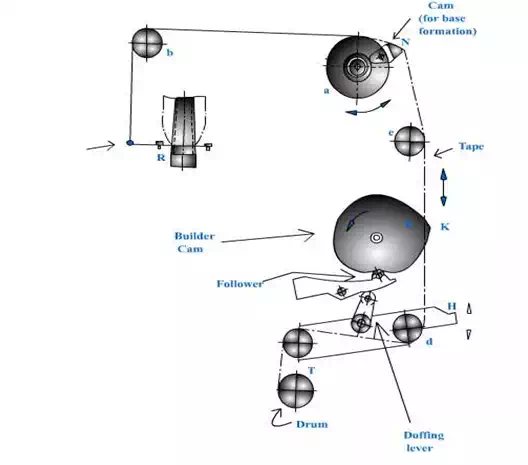
The main layers are the effective cop filling layers. The cross layers are made up of widely separated steeply downward-inclined coils of yarn and are formed during rapid lowering of the ring rail.
They form the separating layers between the main layers and prevent pulling down of several layers simultaneously, known as slough off when yarn is drawn off at high speed in back winding machines. In the absence of such separating layers, individual yarn layers would inevitably be pressed into each other and layer-wise draw-off of yarn would be impossible.
Raising and lowering of the ring rail is caused by the heart shaped cam and is transmitted by chains, belts, rollers, etc. to the ring rail. The long flat part of the cam surface forces the ring rail upward, slowly but with increasing speed. The short steep portion causes downward movement that is rapid but with decreasing speed.
The formation of the base
The heart-shaped cam and the delivery roller are coupled together by the drive gearing. Thus, the length of yarn delivered for each revolution of the cam is always the same. But, due to the presence of the cam N (Figure-4) between the tape and the pulley during the initial stages of cop building, the lift or the height of the layer is shorter to start with. The position and design of the cam N is selected such that the height of the layer increases gradually, till it is moved totally away from getting in contact with the tape. This is attained by winding of the tape on the Drum T for each double layer formation. Once this stage is reached, the heights of the further layers do not change till the end.
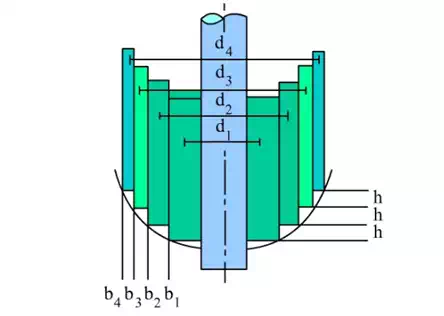
Therefore, the volumes of the individual double layers need to be equal. Deposition of double layers on the tube begins with a small average layer diameter d1. The average diameter increases gradually with each newly deposited layer.
With constant layer volume and increasing height of the layers in the beginning, this can have only one result, namely a continual reduction of the layer width from b1 to b2 to b3, and so on till the height reaches fixed level.
Since the ring rail is also raised by a constant amount ‘h’ after each deposited layer, it follows that curve, rather than straight line, arises automatically in the base portion.
Comments are closed.