For making yarns, there are few stages or process need to be done. Each staple and filaments have different stages and system for the production process.
Filaments
Several common system used by the manufacturer in spinning industry for Filament yarns;
§ Wet Spinning,
§ Dry Spinning,
§ Melt Spinning,
§ Bicomponent Spinning,
§ Biconstituent Spinning
Filament yarns spinning is simplest and least stages require compare with Staple yarns spinning. The molten polymer of synthetic will be inserts into a vessel, after few colorations have been done, the solution will be pushed out through the spinnerets to become filament yarns.
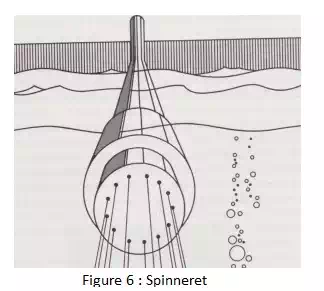
Staple
This process is much complicated and requires several stages need to be done before Staple yarns can be produced. In terms of cost production, it is much higher compare with Filament yarns and this means a lot of energy consumption will be waste during this process.
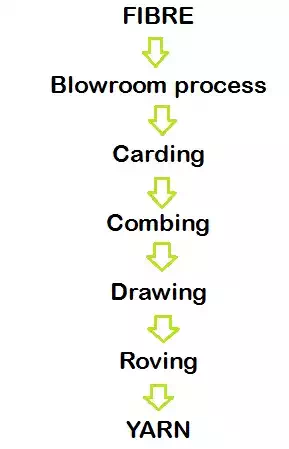
Several common systems used by the manufacturer in spinning industry for Staple yarns;
§ Conventional Ring Spinning,
§ Air-jet Spinning,
§ Open-end or Rotor Spinning,
§ Vortex Spinning
Blowroom
A process where the raw materials packed in bale forms(supplier) will be open and clean the impurities on the surface by using bale opener machine.
Carding
It’s the heart of spinning process. This is where the flock from bales will be open into individual fiber. Thus, it will ease to remove the excess impurities on the fiber surface. At this point, short fiber which not suitable for production in terms of length requirements will be eliminated.
Combing
This is a process where the yarn will be straightened again so that they are arranged in parallel manner. While at the same time, the remaining of short fiber will be eliminated completely from the longer staple fiber. By doing this, long-staple will produce stronger and smoother fabric which are highly demanded in the market.
Drawing
At this stage, it will be pulled the sliver lengthwise direction over each other. Thus, it will cause it to be stronger and thinner in production which is very important in evenness of the yarn. If there is any faults occur during process, it will still pass into the yarn. Most of manufacturer will use blending process where two or more different types of fibers will be blended to form a yarn. Common type of blend use is Cotton/Polyester combination, by doing this it will not only reduce the cost but also increase the performance.
Roving
This is the final stage where the preparatory steps for insertion of the twist. Enough twist is given to hold the fibers together but still has no tensile strength. The roving in bobbins is placed in spinning frame where it passes several sets of roller which running at high-speed to convert into yarn forms.