Fiber-reinforced composites (or fibrous composites) are the most commonly used form of the constituent combinations. The fibers of such composites are generally strong and stiff and therefore serve as the primary load-carrying constituent. The matrix holds the fibers together and serves as an agent to redistribute the loads from a broken fiber to the adjacent fibers in the material when fibers start failing under excessive loads. This property of the matrix constituent contributes to one of the most important characteristics of the fibrous composites, namely, improved strength compared to the individual constituent.
Woven fabrics that are used in composites can be grouped as two-dimensional (2-D) and three dimensional (3-D) structures. 2D-weaving is a relatively high-speed economical process. However, woven fabrics have an inherent crimp or waviness in the interlaced yarns, and this is undesirable for maximum composite properties.
In 2D-structures, yarns are laid in a plane and the thickness of the fabric is small compared to its in-plane dimensions. Single layer designs include plain, basket, twill and satin weaves which are used in laminates. Two-dimensional woven fabrics are generally anisotropic, have poor in-plane shear resistance and have less modulus than the fiber materials due to existence of crimp and crimp interchange. Reducing yarn crimp in the loading direction or using high modulus yarns improves fabric modulus. To increase isotropy, in-plane shear rigidity and other properties in bias or diagonal direction, triaxially woven fabrics are developed in which three yarn systems interlace at 60° angles as shown in Fig. 2. Other
mechanical properties required in relation to different loading conditions are: through thickness stiffness and strength properties, enhanced impact resistance, fatigue resistance,
dimensional stability, fraction thickness, damage tolerance, and subtle conformability.
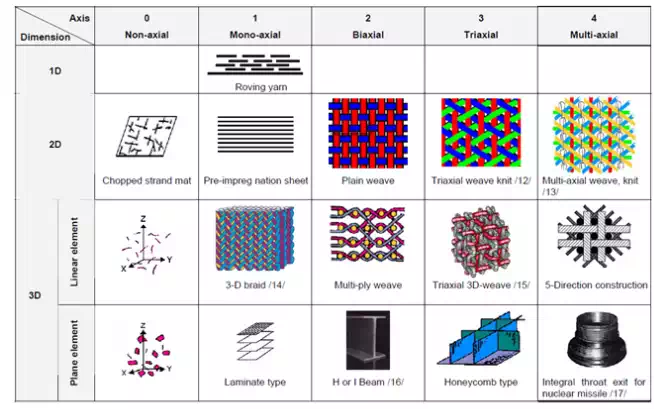
In 3D-fabric structures, the thickness or Z-direction dimension is considerable relative to X and Y dimensions. Fibers or yarns are intertwined, interlaced or intermeshed in the X (longitudinal), Y (cross), and Z (vertical) directions. For 3D-structures, there may be an endless number of possibilities for yarn spacing in a 3-D space.
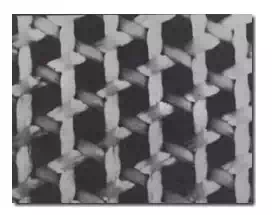
3-D fabrics are woven on special looms with multiple warp and/or weft layers. Fig. 3 shows various 3D-Woven structures. In polar weave structure, fibers or yarns are placed equally in circumferential, radial and axial directions. The fiber volume fraction is around 50%. Polar weaves are suitable to make cylindrical walls, cylinders, cones and convergent-divergent sections. To form such a shape, prepreg yarns are inserted into a mandrel in the radial direction.
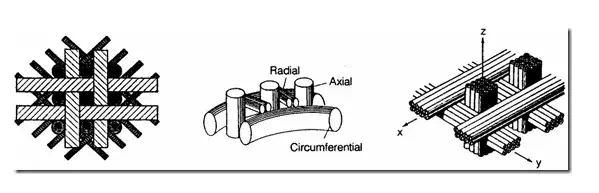
Circumferential yarns are wound in a helix and axial yarns are laid parallel to the mandrel axis. Since the preform lacks the structural integrity, the rest of the yarns are impregnated with resin and the structure is cured on the mandrel. Polar weaves can be woven into nearnet shapes. A near-net shape is a structure that does not require much machining to each
the final product size and shape. Since fibers are not broken due to machining, net shapes generally perform better than machined parts.
In orthogonal weave, reinforcement yarns are arranged perpendicular to each other in X, Y and Z directions. No interlacing or crimp exists between yarns. Fiber volume fraction is
between 45 and 55 percent. By arranging the amount of yarn in each direction, isotropic or anisotropic preform can be obtained.
Except for the components that are fundamentally Cartesian in nature, orthogonal weaves are usually less suitable for net shape manufacturing than the polar weaves. Unit cell size can be smaller than polar weaves which results in superior mechanical properties. Since no yarn interlacing takes place in polar and orthogonal structures, they are also referred to as ´´nonwoven 3-D“ structures in the composites industry. However, it is more proper to label these structures as woven structures with zero level of crimp.
In angle interlock type of structures, warp (or weft) yarns are used to bind several layers of weft (or warp) yarns together as shown in Fig. 4. In place of warp or weft yarns, an additional third yarn may also be used as binder. Stuffer yarns, which are straight, can be used to increase fiber volume fraction and in-plane strength. If the binder yarns interlace vertically between fabric layers, the structure is called orthogonal weave.
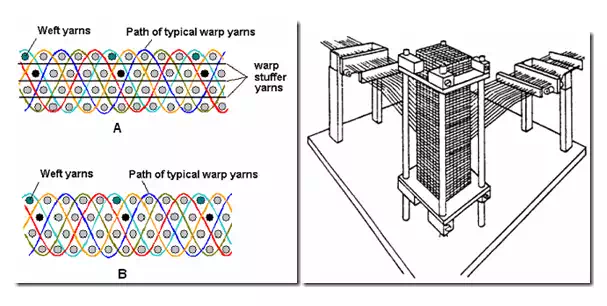
Angle interlock or multi-layer fabrics for flat panel reinforcement can be woven on traditional looms, mostly on shuttle looms. The warp yarns are usually taken directly from a creel. This allows mixing of different yarns in the warp direction. Other more complex 3D-Fabrics such as polar and orthogonal weaves require specialized weaving machines. Several weaving machines were developed to weave complex 3D-structures as illustrated in Fig. 5. Multilayer weaving into a three-dimensional preform consists of interlocking warp yarns in many layers. Whereas in conventional weaving all of the warp yarns are oriented essentially in one plane, in the structure