The tools and appliances used by cotton weaves consist of a spinning wheel (charkha) and a spindle (takli). The cotton is the first ‘separated’ and ‘carded’. A bow shaped beater known as ‘dhun’ is used for the purpose. The string of the bow is placed on the cotton and is made to vibrate by means of a wooden hammer. These vibrations cleanses all foreign matter such as seeds and leaves leaving soft fine cotton behind. The fine cotton is rolled on stick to form a cylinder about half a cubit (6 inches) long and half an inch in diameter.
This is tied to a spindle or takli. The charkha wheel is turned and the thin thread is gently drawn out until it is about 300 yards long and rolled on a charkha which is wound on to a bamboo reel. The yarn is sent to weaving unit where it is woven in to a cloth. After weaving the cloth is calendared with a blunt beater to give it a gloss and to soften it. The cloth is then stamped, ticketed and made ready for sale.
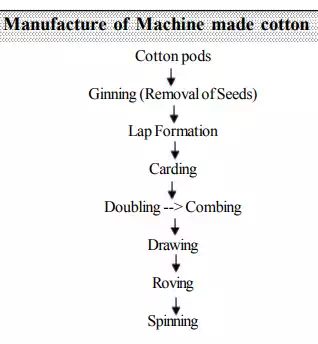
Preparation:
The fibres are first removed from seeds in a gin. This process is called ginning. Every bit of the cotton fibre is used in the manufacture . The fibre mass is then compressed into bales and shipped into spinning mills. The short ends left on the seeds after the longer fabric. Fibres have been removed are used in the production of rayon, plastics, dynamite and many other by products, which are then used in the production of seed oil, hydrogenated fats, soaps and cosmetics
Forming the laps:
In the step dirt from cotton fibre is removed and fibres are made in to a soft roll or lap. Then several laps are combined into one.
Carding:
These fibres are drawn together to form a loose rope called slive
Doubling:
Slivers are combined here for uniformity
Combing:
This process is continuation and refinement of carding process. All cotton yarns for fabrics are carded but not all are combed. Yarns that are combed are finer even and free from all woody stalk of the plant. They are used for finer quality fabrics such as voile and organdie. Fabrics made from these fabrics are expensive too. The slivers are called carded slivers.
Drawing:
The slivers is then combined, smoothened and stretched. The slivers may be drawn reduced further in size and given a slight twist by a process called roving in which the slivers is passed through rollers and wound on to bobbins set into spindles. It is done in a speed frame.
Roving:
The bobbins are placed on the roving frame where further drawing and twisting takes place until the cotton stock is about a pencil lead in diameter.
Spinning:
Done on the spinning frame where the stock passes through sets of high speed rollers and gives the yarn of desired thickness
Weaving and dying:
The yarn is then knitted or woven in any one of the variety of weaves and structures. Warp yarns are usually more strongly twisted than filling yarns since they must withstand greater strain in weaving and finishing. Dye stuffs may be applied to raw cotton, yarn or piece goods
Finishing:
It includes starching,calendaring,sanforizing,mercerizing or other finishes as it is necessary for the particulars use for which the cloth is intended. These finishes may be applied to yarns but are usually applied to fabric. The fabrics may be given these special finishes before or after dyeing