The wet processing is a term that involves the mechanical and chemical treatment to improve the aesthetic value of the fabric, yarn, fibre. The wet processing sector can be divided into three distinct sections.
1) Preparation process or preparatory process.
2) Colouration process.
3) Finishing process.
The general process sequence followed for the fabric wet processing is shown in Figure 11.
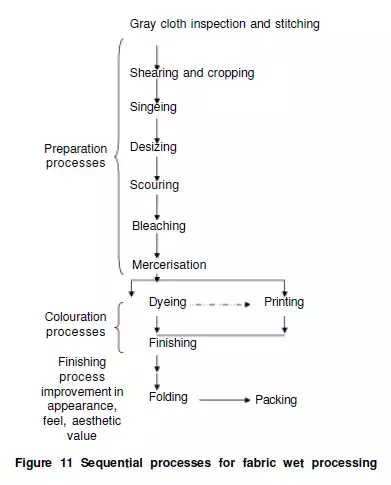
Different sequences in fabric wet processing briefly discuss as follows.
Grey Stitching
Same surface stitched together to make it continuous.
Shearing and Cropping
This process is employed to remove the unevenness present on the surface of the fabric so as to attain even surface for further processing.
Singeing
The singeing process is carried out for the purpose of removing the loose hairy fibres protruding from the surface of the cloth as well as from the interstices fibres of yarn that are burnt away with the help of gas flame, directly impinging on the fabric resulting in giving smooth, even and clean looking face.
There are three types of singeing machines:
1. Plate singeing machine.
2. Roller singeing machine.
3. Gas singeing machine.
The most commonly used machine is gas singeing machine.
Objects of Singeing
1. To provide smooth and even surface for fine prints.
2. To reduce the pilling tendency.
3. To reduce the fuzzy appearance of the fabric.
Desizing
Sizes are applied to the warp yarns of the woven fabrics to assist the weaving process but must be removed prior to dyeing or printing. This process of removing the starch from the fabric is called desizing. Cellulosic and Synthetic fabrics contain sizes to some extent, whereas knitted fabric does not contain sizes.
Sizing is a necessary operation in which the cotton warps are sized to withstand the stress and strains during weaving.
The size is applied depending upon the type of yarn, ie, coarse or fine or the type of twist S or Z. To make the wet processing more efficient, desizing treatment is applied which removes the size content from the fabric.
Starches and waxes present in the size paste forms a hydrophobic film on the surface of the fabric which hinders the further processing such as dyeing, printing. The methods available for desizing are classified in Figure 12. Mostly accepted desizing technique in textile industry are enzymatic desizing as it is very safe and does not cause any damage to the fabric.
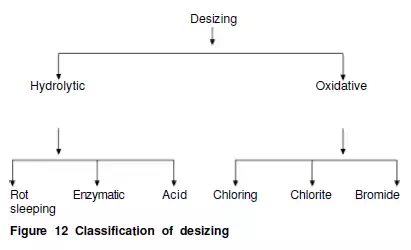
Scouring
Scouring is the next process after desizing in which the water insoluble impurities, the natural fats and waxes present in the fabric are removed. This provides a greater
cleaning action to remove the soiling and staining developed during transportation or storage of the goods. Due to the removal of these impurities, the absorbency of the fabric increases to the greater extent, which facilitates further processing functions.
There are two methods come into account, which are, alkali scouring and solvent scouring.
Normally, alkali scouring is the mostly accepted process and sodium hydroxide (NaOH) is applied as alkali.
Bleaching
The scouring process of cotton removes waxes, but other majority of impurities leaving behind the natural colouring matter. In such situation, bleaching completes the
purification of fibre by ensuring the complete decolourisation of colouring matter. A general classification of bleaching agents is shown in Figure 13.
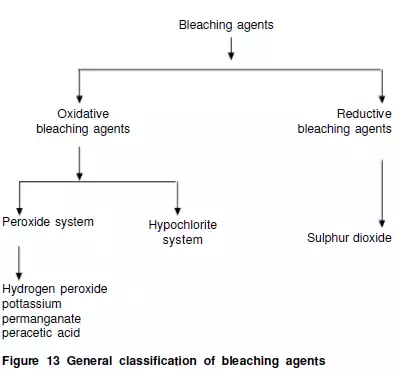
The bleaching process must ensure.
* a pure and permanent whiteness
* level dyeing properties (there should be no variation
in bleaching)
* there should not be any loss in tensile strength due
to degradation of cellulose
* eco-friendly bleaching should be preferred
Mercerisation
This process is named after John Mercer in the year 1884. The main purpose of mercerization is to increases dyeability of cotton fabrics and study the effects of strong caustic dye on cotton. The process is carried out with 118% to 20% caustic soda at 20oC to 24oC.
Objectives of mercerisation are as follows.
* To impart luster.
* To impart dimensional stability.
* To improve the strength.
* To increase the capability to accept dye.
* To make the fabric more absorbent.
* To give soft handle.
The mercerization process is classified as:
Caustic Mercerisation
* Cold mercerisation
* Hot mercerisation.
Liquor Ammonia Mercerisation
Dyeing and Printing
Textiles are usually coloured to make them attractive and beautiful. They would appear extremely dull in the absence of colour. There are two ways of adding colour to a textile
substrate, ie, printing and dyeing. Printing is a process in which a multicolour effect is
produced on the textile at discrete places where as dyeing completely covers the substrate with colour. The substances used to colour the textiles can be classified as
dyes or pigments.
Methods of Dyeing
Batchwise processes: The machine used in this process is jigger, jet dyeing machine
Continuous processes: These methods are specified by continuous dyeing range. The basic units for continuous process are padding, steaming, dry heat treatment and
soaping.
Quality of Dyeing
The major requirements for dyed goods are evenness of dyeing, desired fastness value and brightness of colours. Process controls are necessary to achieve these objectives.
Printing
Printing results multi coloured design effects on textiles. The most economical multicoloured effects on textiles can also be produced by combining dyed fabrics or woven and knitted fabrics using coloured yarn, but the effects are restricted to simple geometrical designs. In printing, there is no restriction to the designer and all types of fabrics in any yarn, pliers or fabrics can be printed. Printing can be combined with white as well dyed fabric grounds. Broadly, printing can be classified into these group.
Flat Bed Screen Printing
The fabric is printed with the first screen and passes to the next screen. In this process all the screens for the design (one screen for each colour) are positioned accurately along the top of the long endless belt, known as a blanket.
Rotary Screen Printing
In rotary screen printing, continuous rotation of a cylindrical screen while in contact with the fabric ensures genuinely continuous printing. The print paste is fed inside of the screen. During printing it is forced out through the design area with the acid of a stationary squeeze.
Heat Transfer Printing
In this case the paper is printed, first and then it is transferred to the fabric at high temperature simply by sublimating the disperse dye. Printing of textiles also contain various styles which can be classified as follows.
Direct Style of Printing
In this style, the print paste is directly applied either by roller or screen and desired motifs with different colours can be obtained. This style is generally applied for all type of print motifs irrespective of no. of colours, coverage of the print paste and the cost.
Discharge Style of Printing
In this style, generally the fabric is dyed all over with any class of the dye and after drying, the same is printed with certain chemicals which destroy or discharge the dyed
colour in the printed portion, which is responsible in giving white portion in the dyed ground. This is called as white discharge effect or style. If a dye which is resistant to the
above chemicals in the print paste is incorporated, the coloured effect instead white can be obtained and is termed as coloured discharge on dyed ground. The chemicals
which destroy or discharge the colour in the printed portion is called as ‘discharging agent’. The dyed colour must have good dischargeability whereas a dye in the printed portion (for getting coloured discharge) must have no dischargeability property.
Resist Style of Printing
In this style, the printing is carried out first with certain chemicals, called as resisting agents and dyeing afterwards. The resisting agents resist for the development
of the colour in the printed portion and produced a white effect. If coloured effect is needed, a dye which is resistant to this resisting chemical must be incorporated in the
printing paste and dyeing follows. In this case, a coloured resist effect is obtained.
Generally discharge and resist styles of printing are applied to the fabric motifs where heavy blocks are used wherein shrinkage of the fabric after printing and cost of the direct style of printing will be very high and hence discharge and resist style of printing is used.
Finishing
Textile finishing covers an extremely wide range of activities, which are performed on textiles before they reach the final customer. The term finishing includes all the mechanical and chemical processes employed commercially to improve
the acceptability of the product. The finishing can be categorised as mechanical finishing and chemical finished.
Mechanical Finishing
This can be further subdevided as calandering and napping.
Calendering
The process referes to compression of fabric between two heavy rollers to provide a smooth appearance and the fabric surface.
Napping and Shearing
This process essentially consists surface shearing and cut the raised naps to a uniform height.
Chemical Finising
As the name implies, this process refers to application of chemicals. These are eight methods for chemical finishing.
1. Water repellency.
2. Flame retardancy.
3. Resin finishing anticrease, wash-n-wear, durable press
(permanent pleating).
4. Softening (handle modification).
5. Oil and soil repellency.
6. Antistatic finishes.
7. Anti-microbial finish.
8. Both proofing and insect damage.