Weaving and dyeing were established in the New World before arrival of the Europeans. Weaving was in an advanced state in North and South America during prehistoric times; both the Peruvians and the Mexicans had fine woven fabrics. The Peruvian fabrics were much like those of ancient Egypt, although contact between the two civilizations is generally considered unlikely. Inca cotton and wool fabrics were brilliantly coloured, with patterns based on geometric and conventionalized human forms. Fabrics, especially blankets, made by the Navajos of Arizona and New Mexico had exceptionally close texture and brilliant colour. English settlers established a cloth mill in Massachusetts in 1638. There Yorkshire weavers produced heavy cotton fustians; cotton twill jeans; and linsey-woolsey, a coarse, loosely woven fabric of linen and wool. Fulling mills were operating in Massachusetts by 1654, freeing the communityfrom dependence on England for fine linen and worsted. The industrydeveloped steadily and received a major impetus from Eli Whitney’sinvention of the cotton gin in 1793.
Effects of the Industrial Revolution
The textile industry, although highly developed as a craft, remained essentially a cottage industry until the 18th century. The advantages of cooperative operations were realized much earlier, and numbers of workers occasionally operated together under one roof, with one such group operating a mill in Zürich in 1568 and another in Derby, Eng., in 1717. Factory organization became most advanced in the north of England, and the Industrial Revolution, at its height between 1760 and 1815, greatly accelerated the growth of the mill system.
John Kay’s flying shuttle, invented in 1733, increased the speed of the weaving operation, and its success created pressure for more rapid spinning of yarn to feed the faster looms. Mechanical spinners produced in 1769 and 1779 by Sir Richard Arkwright and Samuel Cromptonencouraged development of mechanized processes of carding and combing wool for the spinning machines. Soon after the turn of the century the first power loom was developed. The replacement of water power by steam power increased the speed of power-driven machinery, and the factory system became firmly established, first in England, later in Europe and the United States.
From the 19th century to the present
Throughout the 19th century a succession of improvements in textile machinery steadily increased the volume of production, lowering prices of finished cloth and garments. The trend continued in the 20th century, with emphasis on fully automatic or nearly fully automatic systems of machinery.
Application of scientific methods
The mechanical developments in textile production associated with the Industrial Revolution resulted from the application of comparatively simple engineering and physical principles. Further progress required a clear understanding of the scientific principles of textile processing. Lack of basic information on the structure and properties of fibres limited understanding, delaying a scientific approach to textile processing. In the late 19th century, however, increasing knowledge of the physical and chemical properties of fibres led to application of scientific methods. Applications of chemistry originally attracted the greatest attention, largely because of the production of new compounds and the realization that fibres could be considered the result of chemical activity. In the 20th century, with the development of electronics and computers, new physical and engineering concepts were employed in textile research and development. An outstanding application of science to the textile industry was the development of man-made fibres, providing new textile materials and leading to the application of new processes to traditional fibres, thereby providing faster processing methods and introducing a wider variety of new techniques. The man-made fibreindustry originally employed textile expertise developed through years of experience with natural fibres, but the excellent results obtained by the scientific approach encouraged increased industrial use of applied science, and information was soon accumulated on the behaviour of fibres under a variety of conditions.
The modern textile industry
Both industrialized and developing countries now have modern installations capable of highly efficient fabric production. In addition to mechanical improvements in yarn and fabric manufacture, there have been rapid advances in development of new fibres, processes to improve textile characteristics, and testing methods allowing greater quality control. The modern textile industry is still closely related to the apparel industry, but production of fabrics for industrial use has gained in importance. The resulting wide range of end uses demands a high degree of specialization. In the most technically advanced communities, the industry employs technicians, engineers, and artists; and a high degree of consumer orientation leads to emphasis on marketing operations. Some manufacturing operations, usually serving specialized or local markets and dependent on a limited number of firms for product consumption, still employ many hand operations, however.
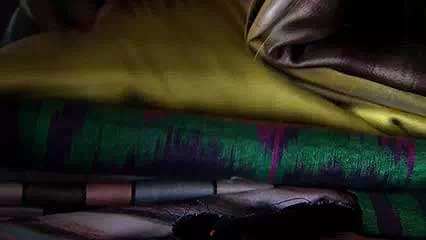
Xinjiang, China: silk productionLearn about traditional silk production practiced by Uighur people in the Uygur Autonomous Region of Xinjiang, China, and how silk is being used in contemporary fashion, 2016
Modern fabrics
The many types of modern textile fabrics, produced from both traditional and man-made materials, are often classified according to structure. Fabrics made by interlacing include woven and knitted types, lace, nets, and braid; fabrics produced from fibre masses include bonded types, wool felt, and needle-woven types; composite fabrics are produced by uniting layers of various types. Conventional weaving and knitting methods are currently the major textile manufacturing techniques, but newer construction methods are achieving acceptance and may replace certain long-established products as costs of conventional textiles continue to rise and rapid technological advances continually develop new materials.
Quality control
Textile fabrics are judged by many criteria. Flexibility and sufficient strength for the intended use are generally major requirements, and industrial fabrics must meet rigid specifications of width, weight per unit area, weave and yarn structure, strength and elongation, acidity or alkalinity, thickness, and porosity. In apparel fabrics, design and colour are major considerations, and certain physical properties may be of secondary importance. In addition, the various tactile properties of a fabric, described as its “hand,” “handle,” or “feel,” influence consumer acceptance.
The textile industry increasingly employs research and development in the area of quality control. Medieval craft guilds were concerned with maintaining high quality standards, and later textile mills established rigid systems of inspection, realizing that a reputation for supplying fault-free goods encouraged repeat orders. Modern quality control has been assisted by development of techniques and machines for assessing fibre, yarn, and fabric properties; by the introduction of legislation regarding misrepresentation in many industrialized countries; and by the establishment of rigid specifications by a growing number of buyers. Specifications have been established for the purchase of industrial fabrics, for textiles used by the military and other branches of governments, and for similar purchasing methods adopted by some retailers and other large buyers. In consumer-oriented areas, the public is becoming aware of product testing and is beginning to require proof that products have met certain test standards.
Many modern textile organizations test product quality at every major stage of processing. Yarns are tested for uniform thickness and other characteristics; fabric pieces are checked for defects; and the fastness of finishes and colours to various conditions is determined. Although it would not be feasible to test each yarn or fabric piece produced, statistical techniques allow maintenance of quality within previously specified limits, and the introduction of automatic testing devices has greatly reduced testing time and cost. Methods for assessing such properties as dimensions, strength, and porosity have been established, and their validity is generally accepted within the industry. Standards are available for colourfastness, although such important properties as water-repellency, resistance to creasing, and flame resistance are presently more difficult to define, and various organizations have adopted their own test procedures. It is important, for example, that a fabric described as flame-resistant should conform to some specification in which the meaning of flame resistance is clearly defined.
Some manufacturers attach trademarks and quality labels to tested goods, and licensed trademarks are often associated with particular processes for which the manufacturer has been granted a license. The terms of the license require the manufacturer to ensure that his products meet the standards laid down by the proprietors of the particular process.
Production Of Yarn
Yarn is a strand composed of fibres, filaments (individual fibres of extreme length), or other materials, either natural or man-made, suitable for use in the construction of interlaced fabrics, such as woven or knitted types. The strand may consist of a number of fibres twisted together; a number of filaments grouped together but not twisted; a number of filaments twisted together; a single filament, called a monofilament, either with or without twist; or one or more strips made by dividing a sheet of material, such as paper or metal foil, and either twisted or untwisted. The properties of the yarn employed greatly influence the appearance, texture, and performance of the completed fabric.
Textile fibres
Raw materials
Fibres are units of matter having length at least 100 times their diameter or width. Fibres suitable for textile use possess adequate length, fineness, strength, and flexibility for yarn formation and fabric construction and for withstanding the intended use of the completed fabric. Other properties affecting textile fibre performance include elasticity, crimp (waviness), moisture absorption, reaction to heat and sunlight, reaction to the various chemicals applied during processing and in the dry cleaning or laundering of the completed fabric, and resistance to insects and microorganisms. The wide variation of such properties among textile fibres determines their suitability for various uses.
The first fibres available for textile use were obtained from plant and animal sources. Over a long period of experimentation with the many natural fibres available, cotton, wool, jute, flax, and silk became recognized as the most satisfactory. The commercial development of man-made fibres began late in the 19th century, experienced much growth during the 1940s, expanded rapidly after World War II, and is still the subject of extensive research and development. This group includes regenerated fibres, such as rayon, made from fibre-forming materials already existing in nature and manipulated into fibrous form, and synthetic fibres, with the fibre-forming substance produced from chemicals derived from such sources as coal and oil and then made into such fibres as nylon and polyester.
Factors affecting cost
The cost of fibres is determined by availability, the kind and amount of processing required, and their versatility. Natural fibres usually require extensive land area for their production, are affected by climatic conditions, and must frequently be transported long distances to the point of manufacture. Because quantity and quality are not easily controlled, prices tend to fluctuate. Research has been directed toward improving various properties during the manufacturing processes. Man-made fibres can usually be produced near the point of use; their production does not require large land areas; they can be manufactured quickly, in desired quantities, with specific built-in properties; and they require little advance preparation for conversion to yarn. Initial costs are high because of the production equipment employed, but prices tend to be stable and may be reduced as production expands. Research has been directed toward improving the properties of man-made fibres and developing types suitable for specific purposes.
Conversion to yarn
Because filaments, such as silk and the man-made fibres, have extreme length, they can be made into yarn without the spinning operation necessary for the shorter staple fibres. When grouped together in a loose, continuous rope without twist, man-made filaments are called tow. Filaments may be loosely twisted together to form yarns of a specified thickness. Staple fibres, such as cotton, only a few inches long, must be tightly twisted together to produce satisfactory length.
Filament yarns are usually thin, smooth, and lustrous; staple yarns are usually thicker, fibrous, and without lustre. Man-made filaments cut to a predetermined short length become staple fibres, usually described by combining the fibre name with the term staple, as in rayon staple.
Treatment of raw fibre
In modern mills, most fibre-processing operations are performed by mechanical means. Such natural fibres as cotton, arriving in bales, and wool, arriving as fleece, are treated at the mill to remove various foreign materials, such as twigs and burrs. Wool must also be treated to remove suint, or wool grease; silk must be treated to remove sericin, a gum from the cocoon, and the very short silk fibres, or waste silk. Raw linen, the fibre of flax, is separated from most impurities before delivery. Man-made fibres, since they are produced by factory operations, rarely contain foreign materials. Blending, frequently employed for natural fibres, involves mixing fibres taken from different lots to obtain uniform length, diameter, density, and moisture content, thus assuring production of a uniform yarn. Blending is also employed when different fibres are combined to produce yarn. Man-made fibres, which can be cut into uniform tow, do not require blending unless they are to be mixed with other fibres. Cotton, wool, waste silk, and man-made staple are subjected to carding, a process of separating individual fibres and causing many of them to lie parallel and also removing most of the remaining impurities. Carding produces a thin sheet of uniform thickness that is then condensed to form a thick, continuous, untwisted strand called sliver. When very fine yarns are desired, carding is followed by combing, a process that removes short fibres, leaving a sliver composed entirely of long fibres, all laid parallel, and both smoother and more lustrous than uncombed types. Slivers may be loosely twisted together, forming roving. Hackling, a process applied to straighten and separate flax, is similar to combing.